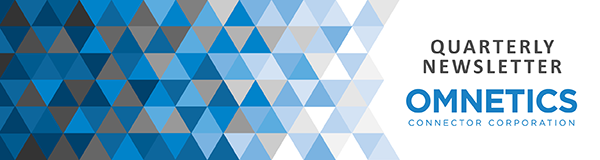
Evolving Nonmilitary Nano-D Applications
As electronic miniaturization becomes more prevalent throughout many industries, the Nano-D connector has proven to be a versatile interconnect style. These connectors originated in the military market, but they are now being used in unexpected and different applications than they were originally designed for. As more markets begin utilizing these high reliability miniature interconnects, the Nano-D has established itself as a player in these diverse applications.
Perhaps one of the most unique areas in which Omnetics is seeing this connector being utilized is within the animatronics and robotics industry. When you step into a ride at a theme park, you’ll see your favorite characters moving around and interacting with you. For every movement an animatronic robot makes, a connector pairing is needed. The animatronics designers previously used cheaply made connectors, but switched to a military-style miniature connector to withstand the repetitive and constant motion of the robotics.
Many people might not think of these animatronic robots as needing highly reliable connectors, but with the many connectors needed for each robot and the high amounts of shock and vibration happening within them, a reliable connection is paramount. In addition, if a connector fails within these animatronics, it can lead to serious downtimes and lost revenue at the park. As soon as the animatronics fail, the rides themselves must close down, which has large implications on revenue. So while there was originally a cost savings in buying cheaper plastic style interconnects, theme parks have serious implications on revenue if these connectors don’t perform. The Nano-D connector is just the answer. While maintaining the high density form factor that allows these connectors to be designed into tight spaces within these animatronics, the high reliability aspect eliminates the chance of failure. Utilizing the Omnetics flex pin design in conjunction with meeting the strict standards of the Mil 32139 specification, the Nano-D connectors have experienced zero failures since introduction into these parks.
Another nonmilitary style application that Omnetics is seeing significant growth in is the space industry, whether it be for communication, navigation, or earth observation. Satellite companies used to send giant school bus sized satellites into orbit (not much need for a miniature connector there). Now, companies are learning they can get the same functions of these satellites by sending constellations of small satellites into low earth orbit. The launching and building of these small satellites is much more affordable and realistic than putting all your marbles into one larger satellite. The shrinking of the technology allows the Nano-D to come into play. The ability to stack multiple boards and run high signal counts in condensed areas allows these manufacturers to meet the strict size demands that these satellites require. Combined with the additional space level screening per NASA EEE-INST-002, these Nano-D’s are proven to meet the shock and vibe requirements that the payload will face getting up to orbit.
Both of these applications are key examples of how the Nano-D continues to expand its wide variety of uses. As long as the need for miniaturization or high reliability is a factor, the Nano-D will continue to be a leading option. Check out our Nano-D connector options for reducing size and weight.
Micro-D and Nano-D Backshells
Circuits are constantly improving to serve new applications for a wide range of electronics—from portable robots to surgical monitoring, control circuits and on to key military systems. As circuit signal speeds increase and are reduced in size, the proximity of the signal-to-signal interference and crosstalk can become an issue. Mil-Spec connectors and cabled interconnections are used in a variety of mission critical and high reliability applications ranging from military avionics, unmanned robotics, satellites, and soldier worn systems. Adding a backshell to the interconnect design helps protect sensitive electronics from EMI and crosstalk as well as providing a mechanical strain relief for the wires or cable.
A backshell is a separate metallic piece that screws onto a Micro-D or Nano-D connector shell. It can be added at any point prior to the completion of a wire harness or cable assembly. For a more robust solution, integrated backshells can be used. An integrated backshell is machined as part of the Micro-D or Nano-D housing. This solution provides 360 degree EMI shielding and eliminates the need for screws. Because integrated backshells are an integral part of the connector housing, they are more secure and take less time to assemble.
Micro-D and Nano-D back-shells are designed to protect the back end of the connector. Backshells provide strain relief to the cable or wires, which, in extreme environments, prevents mechanical stress and damage to the contacts. Connector backshells also provide additional EMI protection when they are used as a grounding point for the cable shield, a ground wire, or when braiding is added over the wires. Often times, with a backshell, random electrical signal noise is bled off the cable and shell onto a grounding circuit.
Many design formats are available for Micro-D and Nano-D backshells, including two piece solutions, straight, 45°, 90°, oval or round wire/cable exit, and with two distinct wire/cable exits. These backshell designs are available for all standard Micro-D and Nano-D connector configurations, or they can be modified to meet the specific design requirements or challenges. For high reliability, mission critical applications where a standard backshell will not work, customized backshells can be designed and machined to specific shapes and functions to meet the specific design requirements or challenges of an application.
From the Engineer’s Desk: High Speed Connector Design
Coax Strengths and Challenges
Coax cables and connectors are used in a wide range of applications with various purposes. In the third and final installment in our series on coax cables and connectors, we will discuss the strengths and challenges of the coaxial topology.
Strengths of Coaxial Cables and Connectors
One of the biggest strengths of the coaxial construction is its excellent insertion loss. This is mainly achieved through a constant, controlled impedance. The impedance is controlled by providing an environment where the distance between the signal (inner conductor) and the ground (outer shield) remains constant. Combined with the use of a high performance, low dielectric insulation material such as PTFE, coax yields a solution with excellent insertion loss. Currently, there are various coax solutions for frequencies up to 110 GHz, so there are solutions for nearly all applications.
Another strength of coax is its isolation, which comes in three main forms: crosstalk between adjacent signals within a system, transmitted EMI (emissions) that exit to the outside world, and received EMI (susceptibility) which enter from the outside world. In all cases, the coax topology yields excellent isolation by fully encapsulating the signal conductor inside the outer shield. In theory, this construction provides a perfect shield to the outside world. In reality, there is always some leakage depending on the effectiveness of the outer shield. Various shielding options are available depending on the level of required shielding effectiveness. A single braid yields about 50-60dB, while a braid and foil yields around 90dB. For very sensitive applications, additional braids/foils are used to further improve the isolation.
Lastly, another strength of coax is its versatility. Coax is generally understood to be used for analog signaling, but some video applications also use coax.
Challenges of Coaxial Cables and Connectors
One of the biggest downsides to coax is its size. Though coax contacts are available in many sizes, they are larger than other topologies such as discrete wire or twisted pair. This is due to both the impedance requirement (which dictates the size of the insulator) and the shielding requirements (which require a 360⁰ shield around each signal). In other words, the strengths of the coax often make its use challenging. To get an understanding of size, Omnetics Nano Coax contacts are spaced at 0.125”, and only a single row is available. By contrast, standard Micro pins are spaced at 0.050”, Nano contacts are spaced at 0.025”, and both can be dual row. Even if differential pairs are used – with two lines used for each signal – the overall size per signal is significantly smaller than coax.
Coaxial contacts are also challenging to assemble. Proper assembly has a significant impact on the performance and must be done with care. As frequencies increase, the precision of the assembly must increase accordingly in order to achieve a high level of performance.
Challenges of Coaxial Cables and Connectors
Coaxial cables and connectors are used in all sorts of industries and applications. This three-part series provided an in-depth look at coax, including impedance, the purpose of coax contacts, and their strengths and challenges. The goal of the series is to provide a deeper understanding of the uses for coax and assist engineers in selecting the correct coax connector with confidence.
Did you know?
Small Satellites cost about $35,000-$45,000 to launch, making space and weight some of the most important factors in small satellite design. Check out our Nano-D connectors that are perfect for reducing size and weight in space applications.
Calendar of Events
10-13
DSEI
Location: London, UK | S1-100
19-21
Space Tech Expo Europe
Location: Bremen, Germany | Stand A20