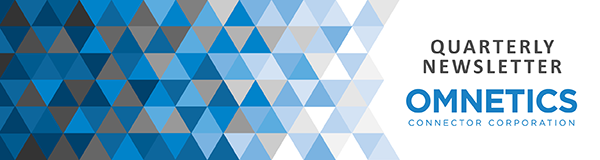
Connectors for Dummies
See the original article in International Design Engineer !
If it’s not broken, don’t fix it, right? But when there’s a way to make it better, engineers can get it done. In a complex system, the tiniest components play critical roles, so refining a product can start with its smallest elements. Slice6, a miniature data acquisition system manufactured by Diversified Technical Systems (DTS), depends on a small connector unit to collect, store and transmit data from sensor arrays in military and automotive crash-test dummies. This connector unit needs to be both rugged and reliable to perform in extreme shock, vibration, and blast environments – it’s all in a day’s work for test dummies used in injury biomechanics testing. Reliable connector performance, however, didn’t satisfy the company that supplied the unit when its engineers realised the custom unit could be made even better.
The custom connector unit, made by Omnetics Connector Corporation, consists of a U-shaped metal shell with two integrated connectors: one Micro connector with 36 pins positioned inside the shell, and one Nano connector with 36 pins positioned on the shell’s exterior. The width of the shell measures just 13mm. The unit fits inside the Slice6 DAQ module, which measures 24 x 30 x 10mm and weighs in at 28g. Size, weight and product availability are key considerations when designing the connector unit. Military orders can be time-critical and the connector unit, made exclusively for DTS, took 10 days to manufacture in small batches of 100 or 120 pieces – not an unusual task for the connector supplier, which specialises in MIL-spec, medical and precision miniature interconnects. Even so, this was a longer lead time than the company liked to quote.
“To manufacture the old version of the unit, we were cutting wires to about 25mm, stripping them on both ends and then crimping a Nano contact on one end and a Micro contact on the other. Each unit contained 36 wires,” says Travis Neumann, special projects manager at Omnetics. “Prepping the wire took about three days. Then we loaded the wires into the connector housing. It took another three days to get all the wires loaded into the two connector pieces that go into the metal shell. After that, we epoxied the connectors to the shell and tested the unit. Overall, it was a time consuming and inefficient manufacturing process.”
Quality control is critical. Slice6 supports NHTSA and EURO NCAP testing, and meets SAE J211, ISO 6487and FAA data acquisition requirements. There is no margin for error. Yet, inside that tiny housing there was a cumulative .91m of wire handled by at least six people. “When a part has a more complicated pin-out, there is a greater risk of getting things crossed. So we always test each piece,” says Neumann.
The engineering team wanted to trim that lead time, plus eliminate the potential for pin-loading error. The solution came in one easy piece: a tiny flex circuit. “Now we make a surface-mount style Micro connector, load the contacts into the plastic pin housing and fill it with epoxy. On the Nano side, we do the same thing,” says Neumann, whose background in hybrid microelectronics exposed him to flex circuitry’s potential uses in connector design. “The flex board arrives 100% tested. When we solder the contacts onto the flex board, our fixtures don’t allow us to put the parts on incorrectly. Finally, we do an IPC visual inspection after they are soldered and then test the parts.”
The time savings are significant: a 120-piece order can be made in about four hours. “This allows us to meet our just-in-time (JIT) supplier goals to reduce inventory and shorten our lead times,” says Grant Newton, Mechanical Engineering department manager at DTS. The flex board is more costly, but the labour savings are considerable. Plus, replacing that expanse of wire with the tiny flex board enabled Omnetics to reduce the size of the unit by 3.17mm, which in turn allowed DTS to fit the Slice6 into tighter spaces.
“We were surprised that Omnetics was able to fit our requirements into an even smaller space. This allowed our customers to fit our products into even tighter locations, so it was a big win for everyone,” says Newton. “Omnetics provided us with details about how the product was being manufactured, which allowed us to discuss the changes from a more informed viewpoint. The engineering team is always open to discuss new designs with us. We consider them an extension of our design team.”
One more advantage of redesigning with flex is, naturally, flexibility. Although DTS originally designed its product for crash dummies, it is now being embedded on helicopter rotors and other devices that gather data that allows manufacturers to make cars, planes, child seats and other vehicles safe. Pretty smart, for a bunch of dummies.
Precision Machining Division Expands with Two New Machines
Omnetics has recently acquired two new machines at our Precision Machining Division location. A Tornos CU2007 and a Tornos GT-32 were purchased for manufacturing rectangular and circular housings, respectively. These machines allow Omnetics to save time and money in our manufacturing processes. The Tornos CU2007 is capable of machining a finished latching Micro-D housing in one simple step, whereas previously, each part needed inspection and rotation up to 5 times. Additionally, the CU2007 allows Omnetics to produce parts with a 5 axis capability, such as backshells with non-standard angles.
Acquiring the Tornos GT-32 is part of a larger effort at Omnetics to reduce outsourcing manufacturing. Our circular housings can now be manufactured in-house, which reduces setup time, decreases lead time, and passes on savings to the customer.
These machines were chosen based on a statement of work developed after evaluating Omnetics’ business needs. It specified what types of parts we would produce, coolant type, collet style, materials, and a considerable number of other details. There were also conditions for acceptance based on performance of the equipment and process stability. The recent expansion of our Precision Machining Division gave us ample space for new equipment and capabilities.
The new Tornos CU2007 and GT-32 machines allow Omnetics to reduce setup time, decrease scrap, run with less operator intervention, lower costs, and decrease lead times. They also allow Omnetics to experiment with new product development and increase our ability to manufacture application-specific parts.
Today’s Electronics Call for Rapid New Connector Development
See the original article in Connector Supplier!
We are in a period of rapid technology development, as designers create new products and instruments with high-speed circuit chips that run faster, last longer, and go places we could not imagine just a few years ago. Often, these products call for original connector designs.
Today’s electronics — equipped with innovative new sensors, detectors, monitors, and communicators — are dominating our businesses, militaries, medical clinics, and daily lives. These products are also inspiring great advancements in connector and component designs. Standard commercial off-the-shelf (COTS) connectors are a great resource for quick prototypes and reference designs and still meet many of today’s application needs. However, as technologies evolve to meet new demands, including higher speeds and smaller sizes, standard connectors don’t always meet the design requirements. In these cases, original connector designs are needed.
Omnetics’ PZN Polarized Nano Connectors are some of the smallest mil-quality, board-to-cable connectors available in the industry. These ultraminiature, high-reliability connectors are available in both COTS and custom versions, as well as a variety of wired and board-mount options.
Connector modules destined for use in today’s electronics frequently require increased miniaturization, demand less current flow, and must meet new, more challenging form and fit parameters while still delivering as much — if not more — functionality as bigger, older models. Meeting these various demands often requires entirely new connector development.
Wearable tech is one application area in which system demands are pressing designers to generate original connector designs. These small devices require connectors that reduce space and weight while increasing the instrument’s capabilities, portability, and ruggedness. Interconnect systems bear much of the wear and tear in plug-and-play systems that endure multiple disconnect and reconnect cycles as components are interchanged, and both durability and secure connectivity are paramount when cables are draped around a piece of equipment or a person.
The Case for Original Connector Designs
Custom design of micro- and nano-miniature connectors used to be perceived as expensive and painstakingly time-consuming. However, today we have fast-turn solid-modeling, 3-D fabrication equipment, and direct-linked CNC machinery. Now metal or polymer shells and insulators can be made within a day or two, after agreeing on the format. By using existing metal interconnection elements, original connector designs and assemblies can be completed very quickly and at significantly lower cost than before. Many connector companies are staffing rapid-turn prototype laboratories with technical specialists to leverage these new capabilities and satisfy these new interconnect challenges.
It is important to realize that key shifts in chip technology and higher-speed digital design are significantly changing the interconnection world. Much of an interconnect’s electrical performance depends on the cable and wiring methods used. Large-wire analog circuitry has its place, but it’s staying in that place. Meanwhile, the market for smaller-diameter cable made with more flexible cabling materials is booming. In many precision systems, both the cable and connector are designed specifically for that application. For example, in the field of prosthetics, one can now see wires from an ECG-type connector routed to operate a complete robotic hand.
New Connector Development Builds Better Connectors Fast
Today, designers working on new connector developments can specify parameters such as size, weight, and shape before deciding on a product format that will meet the product designer’s needs. Typically, the electrical parameters will pre-determine the size and type of the connector’s pin-and-socket system and cable design. For example, a standard digital signal running at less than 13 volts and using less than 100 milliamps would allow for an original connector design loaded with nano-sized pins and connected to 32-gauge wire.
If high reliability is required, a pin and socket set could be borrowed from those used in military specification connectors that have been accepted as QPL products and deliver field-proven performance. In addition, insulators for new connector development — the inner portion of the connector that contains the pin and socket sets — can often be borrowed from current connector designs.
Newer versions of liquid crystal polymers (LCPs) enable more rugged and temperature-resistant insulator and housing options for miniature and nanominiature connectors than many legacy materials. LCP materials can also accommodate an extensive variety of sizes and shapes to better meet today’s new fit and form demands. New LCP insulators can now be made in soft molds to provide first article components, which allows design engineers to test-out a system much faster than the eight- to 10-week lead-times for new insulator and other component designs that were typical not long ago. Connector housings, unique shell shapes, locking mechanisms, and even backshells can now be quickly machined on linked CNC systems and combined with quick assembly and wire connections to provide rapid prototypes of both original connector designs and corresponding cable assemblies needed for new technologies.
These new processing capabilities make it easy to optimize original connector designs to help reduce size and weight, adhere to specific form and fit parameters, and even improve the functionality of portable electronics. In just two to three days, a new solid model drawing can now be sent to customers for review and, after approval, it generally takes less than three or four weeks to completely assemble a new connector and its corresponding cable harness.
These processes also enable significantly lower costs and faster delivery than the redesign methods of days past. The ability to put solid-model drawings in designers’ hands at the beginning of the connector design process supports quick review and approval and reduces both costs and time-to-market. These precision models also help achieve a very high acceptance rate for original connector designs. Then, after rigorous testing in the actual application, the move to production of higher volumes can begin, just as quickly, hastening the delivery of new technology to markets worldwide.
Did you know?
Crash test dummies contain three types of instrumentation: Accelerometers, Load sensors, and Motion sensors. Take a look at our ruggedized connectors for crash test dummies today, or contact us for custom connector parts. (How Stuff Works)
Calendar of Events
19-21
Space Tech Expo Europe
Location: Bremen, Germany | Stand A20